Built-Up Roofing (BUR): An In-Depth Look at Its Pros and Cons
Built-Up Roofing (BUR): An In-Depth Look at Its Pros and Cons
First invented in the 1800s, Built-up roofing (BUR) has become an integral part of flat roofing systems, especially in the commercial sector. You might have seen these roofs over multiple high-rise buildings, warehouses, or offices without even realizing it. This roof resists punctures and extreme weather conditions and creates a watertight surface.
Despite the benefits, it also has a set of drawbacks worth considering before you finally choose a build-up roof for your business. In this guide, we’ll explore the ins and outs of built-up roofing to see if it’s worth the investment!
What is a Build-Up Roof?
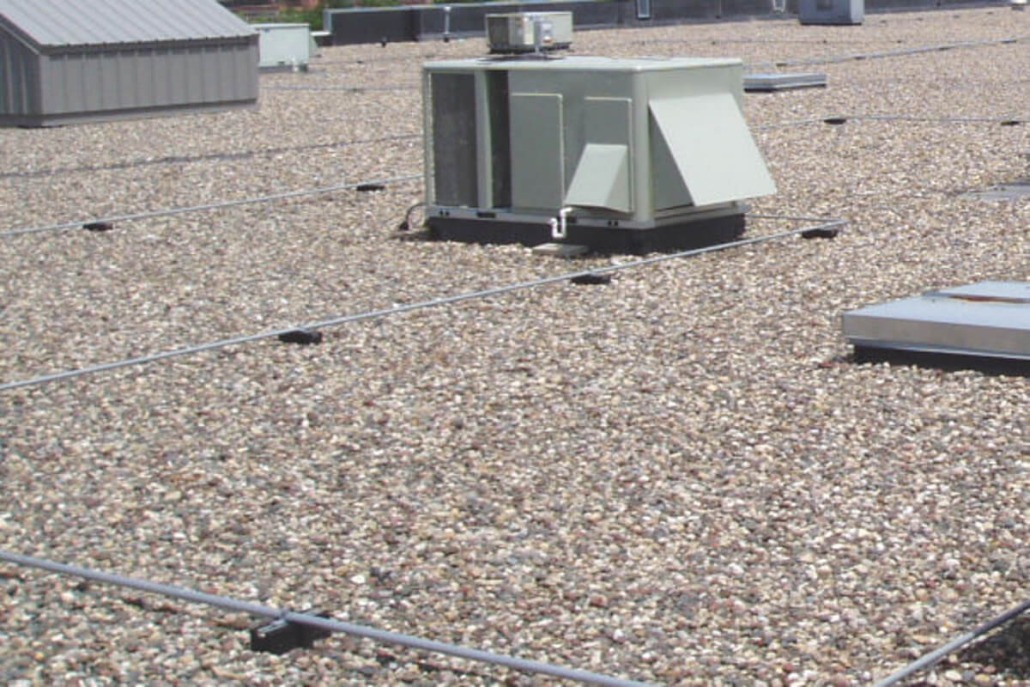
Built-up roofing, also known as tar and gravel roofing, is a conventional roofing solution that is most popular for commercial settings. The name ‘built-up’ reflects how the roof is installed, i.e., by building layers one by one till the desired thickness level is met.
While its legacy dates back over 100 years, due to its durability, this multi-layered roofing system has become popular over the centuries. It’s an incredible way to extend your commercial roof’s life. Here’s a quick overview of the three different types of built-up roofing:
Hot Built-Up Roofing
Well, hot built-up roofing is one in which layers of asphalt are heated until they melt and then spread over layers of ply sheet. While this method is effective, it’s super weather-dependent since it requires the asphalt to stay hot.
Cold Built-Up Roofing
This method is more efficient than hot built-up roofing, and it’s easy to see why. Instead of melting asphalt, roofers use a cold adhesive to bond the ply sheet and the layers together. Since cold BUR is weather-resistant, it’s quite popular for roofing today.
Ballasted Asphalt Roofing
Unlike the other two roofing systems, ballasted asphalt doesn’t require an adhesive to hold the layers together. Instead, the layers of asphalt are held together by placing a heavy layer of gravel on them. This method helps the roof stay durable, even when the weather gets extremely harsh.
Basic Components of a Built-Up Roof
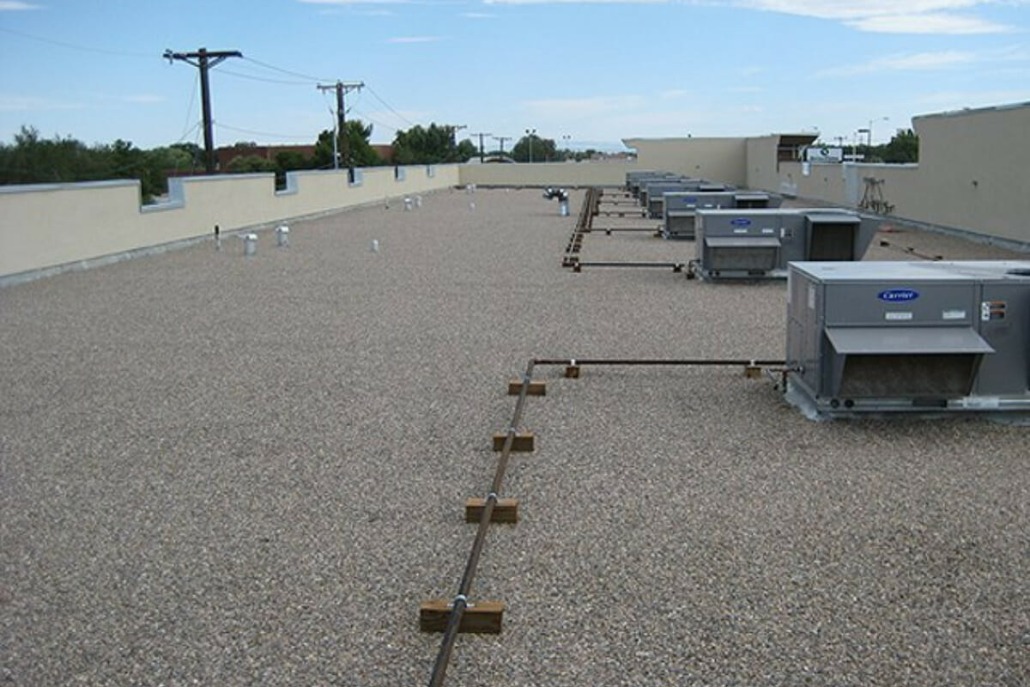
Although modern advancements have played their roles in flat roofing systems, the basic components or layers of a built-up roof have remained unchanged over the years. A typical built-up roofing system usually includes the following main components:
- Base Sheet: As the name suggests, this is the first layer applied directly to the roof deck. This sheet serves as the primary waterproof layer, which sets a solid foundation for the subsequent layers. Typically, it’s made up of fiberglass, polyester, and asphalt-coated organic sheets.
- Ply Sheets/ Felt or Fabrics: Next up, the ply sheet, known as the roofing felt made with reinforced fabrics, is added on top of the base sheets. These felt layers might also be infused with organic materials and are meant to offer extra durability and strength to the roof.
- Bitumen: The basic waterproofing material is the bitumen, which can either be asphalt or coal tar pitch. It bonds the layers together reliably, acting as a tight, water-resistant seal that essentially makes built-up roofing so popular among folks today.
- Surfacing Materials: While it depends on your budget and your building’s requirements, the final layer is usually topped with gravel, slag, mineral cap sheets, or other protective coating materials. Its primary goal is to protect against UV rays and let your newly installed roof last longer.
Benefits of Built-Up Roofing
The built-up roofing system has been around for long, even before it took the modern form it has today. It’s especially popular for commercial buildings that require efficient and reliable roofs. While it’s a solid roofing system, first-timers might be skeptical about whether it’s the right choice.
To save you the legwork, we’ve put together the benefits of built-up roofing that make it worth the investment:
Durability
The most obvious benefit of build-up roofs is their impressive lifespan, ranging from 15 to 40 years, depending on how well you maintain them and the local weather conditions. BUR can efficiently handle extreme weather conditions, which keeps them from cracking over time.
The multiple layers of bitumen create a reliable, waterproof surface that prevents water from seeping into your building. The best part, if your area has extreme weather, you can even top the asphalt layers with tougher materials so your roofs can last longer.
Low Maintenance
Another perk of built-up roofs is that they require minimal maintenance, which is primarily why building owners love them to this date. Although small repairs might be needed over time, you won’t need to replace them fully for many years.
While they’re low maintenance, it’s still recommended to check them once or twice a year for any cracks or pooling water. This lets you address minor issues timely before they turn into huge roofing problems.
Cost-Effective Roofing Solution
When considering the costs of roofing solutions, built-up roofs take the lead among the most affordable systems out there. This explains exactly why they’re the top pick among commercial and industrial building owners.
While multiple factors determine its price, a typical built-up roof costs around $4 to $10 per square foot. The cost-effectiveness, when combined with low maintenance, makes it a smart investment, especially if you’re on a budget!
Fire-Resistant
The top layer of aggregate, such as asphalt and gravel, makes BURs incredibly fire-resistant. This feature is especially desirable for industrial settings, keeping fire from spreading to the building. Coal tar, the most common component of BURs, is especially flame-resistant and requires a very high temperature to ignite.
Plus, the multiple layers of bitumen make these roofs not just durable but also resistant to strong winds and fire.
Energy-Efficient
Modern BURs are known for their energy efficiency, which is super beneficial in hot climate zones. The rigid insulation layer reduces heat transfer, mainly due to the reflective layer that deflects UV rays. The result? Commercial settings remain cooler and maintain more stable indoor temperatures for operations.
The efficiency also means less reliance on heating and cooling systems, which ultimately cuts down on utility costs. This makes it the top choice for eco-conscious building owners.
Cons of Built-Up Roofing
Given the myriad of benefits it offers, it’s pretty obvious that installing a built-in roof can be a smart solution for your building. But, like everything else, these types of roofs don’t come without their downsides. So, before you make a decision, make sure you’ve read through the setbacks to know what to expect from this roofing system:
Lengthy Installation Process
Since the system requires multiple layers, it’s often pretty complex and time-consuming to install a built-in roof. For the best results, it’s best to turn to professional roofing services. These professionals know what it takes to apply bitumen and other layers properly, especially when dealing with hot-applied bitumen.
Odor & Fumes
Before you opt for built-in roofs, it’s worth noting that the installation process emits toxic fumes, which might take a toll on your health. This is concerning for both installers and occupants of the building. Worse yet, the fumes might stay long after the installation, causing discomfort. This is especially true in the case of hot-applied BUR systems.
Relatively Heavier
A notable downside of BURs is that they’re heavier than other roofs, so your buildings often require well-engineered frames or additional structures to support the weight. In case you’re wondering, the higher weight comes from the multiple bitumen layers added for durability.
If your building is older, you’ll require structural reinforcement before installing a built-in roof system.
Hidden Leaks
Another potential downside of BUR systems is the damage caused by freeze-thaw cycles. Water seeping into small cracks leads to cracks, which ultimately causes leaks. So, it’s best to check for warranty with your installers well beforehand. What’s worse is that checking for leaks is more complex than fixing them, mainly due to their multi-layered structure.
FAQs
How Long Does a Build-up Roof Typically Last?
On average, built-up roofs last anywhere around 20 to 30 years. However, their overall lifespan depends a lot on the quality of installation, their maintenance, and the number of layers included. More layers mean a longer lifespan!
How Much Maintenance is Required for Built-Up Roofing?
Although built-up roofs require less maintenance than other roofing systems, frequent upkeep is advisable to keep them intact for years. For instance, routine checks (preferably thrice a year) extend their lifespan and stop minor issues before they grow into big problems. Remember to replace any worn flashings and keep the roof deck away from debris build-up.
Can a Built-Up Roof System Be Installed Over an Already Existing Roof?
Yes, you can install a build-up roof system over an already existing roof, but it’s not always the best idea. To make it a success, ensure that the current roof’s structure is solid and the shingles are both flat and intact.
Conclusion
Built-up roofing is a pretty dependable and pocket-friendly solution for flat or low-slope roofs in industrial settings. The best part about them is that with regular maintenance, they can fend off your roofing worries for decades.
That said, it’s important to be aware of the pros and cons of BURs before making a decision. This lets you prepare for any setbacks beforehand!
If you’re ready to get your built-up roofing system up and protecting your building, there’s no better option than Commonwealth Roofing Corp. Contact us today and let us take care of your roofs already.